THE FRONTRUNNER IS BORN
The Company assembled a talented group of out of the box thinking engineering and design professionals. The team represented a mix of large OEM auto manufacturering and heavy-duty Transit bus experience. The design goal was simple-every component and element of the design had to meet three criteria-Lightweight, Strong, and Durable. Every design element was carefully measured against this set of criteria along with the design goal of providing the most efficient and comfortable lowered floor bus in its class.
In the Spring of 2017 the Frontrunner® was introduced to the bus community at BusCon. Among its notable achievements in design and construction are:
Purpose Built Lowered Chassis
By removing the frame rails of the cutaway and discarding them, the Frontrunner®’s lowered floor structure is bolted in place forming a 93” wide spacious flat floor foundation able to accommodate 15 passengers and up to 3 ADA wheelchair positions in a design just under 23’ in length. Manufactured from high alloy lightweight steel from Nucor (USA), the steel has twice the strength of cold rolled steel at 1/3 the weight allowing higher strength to be achieved with a thinner gauge and less overall weight. Characterized by its unique ability to flex, this construction provides a superior ride without the tendency to crack like cold roll steel which becomes brittle as it becomes thicker in gauge.
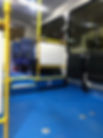

Frontrunner®'s purpose built rear axle is 6” wider on each side improving its already tight turning radius and pushing the wheel wells toward the outside of the bus insuring that all passenger foot room is unencumbered.
Its optional four corner air suspension with ECAS (Electronically Controlled Air Suspension), high quality air dryer, and premium Continental air bags, provides a smooth rattle free ride and kneels to a best in class 9.75” achieving an easy step-in to a flat floor and the lowest ramp angle in the industry. The bus can be driven in the kneeled position if necessary and will raise to its ride height of 12” automatically when the bus hits 5 m.ph with the ECAS suspension system.
Standard air suspension also kneels in the rear and embodies the same rear suspension components of the full air suspension without the full electronically controlled system.
Hot Dip Galvanized Chassis
The Frontrunner®’s purpose built lowered floor chassis undergoes a hot dip galvanization process unique to the bus industry in this size class representing the highest and most Superior form of rustproofing available. Traditional spray on galvanizing merely treats the surface metal with a coating of zinc that can flake and often does not cover the entire surface particularly where surfaces intersect and in joints.
According to Wikipedia “The process of hot dip galvanizing is a form of galvanization in which steel is coated with zinc, which alloys the surface of the base metal when immersing the metal in a bath of molten zinc at a temperature of approximately 840°F. When exposed to the atmosphere, the pure zinc reacts with Oxygen to form Zinc Oxide, which further reacts with Carbon Dioxide to form Zinc Carbonate.”
This protective coating alters the molecular surface structure of the steel and creates a Superior corrosion resistance surface with healing properties. “zinc is a more electropositive (active) metal in comparison to steel. This is a unique characteristic for galvanizing, which means that when a galvanized coating is damaged and steel is exposed to the atmosphere, zinc can continue to protect steel through galvanic corrosion (often within an annulus of 5 mm, above which electron transfer rate decreases).” In short, a hot dipped galvanized product has superior abrasion characteristics relative to other methods including undercoating which have extremely low abrasion characteristics and spray forms of cold galvanization which can flake and peel leaving the underlying metal unprotected. Consider abrasion from rocks, dust, and other road debris.
The bottom line is that Hot Dip Galvanizing provides more than 30X the protection of traditional corrosion resistance methods including undercoating and spray on cold galvanization.
Hot Dip Galvanizing provides more than 30X the protection of traditional corrosion resistance methods including undercoating and spray on cold galvanization.
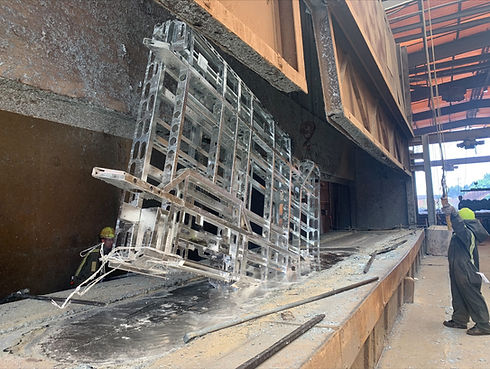
Original prototype Frontrunner® lowered floor chassis sitting outside for over 4 years, RUST FREE!

The entire lowered floor structure is hot dip galvanized representing the most superior form of corrosion protection available in a cutaway sized mini-bus. Eliminating the need for ineffective and potentially detrimental undercoating, the hot dip galvanization process alters the molecular structure of the surface metal.
In addition to providing superior corrosive protection from salt, road debris, and water the process provides “self healing properties” to the steel it protects. Should a rock or piece of road debris scuff the surface of the metal, the exposed zinc which has become part of the metal heals itself when exposed to the air. This is a vastly superior form of corrosion protection when compared to other industry methodologies which are largely sprayed on galvanization.
Fully Composite Lightweight Modular Bus Structure
The fully composite bus structure of the Frontrunner® incorporates a patented high density closed cell foam panel with integrated pultrusions for additional strength along the sidewalls and door frame. Utilized for outdoor structural projects including bridge building, pultruded beams are significantly lower in weight than square stock steel and much stronger.
This patented and unique approach to bus body structure provides the highest strength to weight ratio available in the industry today. The entire structure including the front bulkhead panel, side walls, roof, and aluminum roof extrusions are bonded with the latest in structural high strength adhesives, achieving a structure whose overall strength is much greater than the strength of its individual parts. Integrated rain gutters in the roof extrusions designed to channel water to the rear of the bus eliminate the need for unsightly drip moldings over the windows.
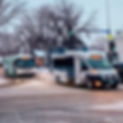